





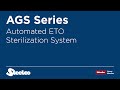
Ethylene oxide sterilizer
The AGS Series of sterilizers using Ethylene Oxide represents the best relationship between engineering and quality price, operating running costs, and, most important, the safety of the system and operators. AGS Series has been designed for low-temperature sterilization of heat-sensitive products according to the EN 1422 Standards for the medical processing industry, such as plastic syringes, perfusion sets, dialysis cartridges, heat-sensitive rubber products, and specific surgical instruments.
This range of Ethylene Oxide sterilizers are available in two versions:
- AGS series | Pressure sterilization program – up to 10% of Ethylene Oxide, with the remaining 90% made of inert gas (normally Nitrogen)
- AGS-E series | Vacuum sterilization program – up to 90% of Ethylene Oxide, with the residual 10% made of inert gas (normally Nitrogen)
Following customer requests, dedicated chambers for separate processes can be supplied: Pre-conditioning, Sterilization, and Degassing chambers.
Sterilization process
EtO sterilization process involves three different phases, which can be carried out within a single sterilization chamber or divided into three different work cells.
- Pre-conditioning: The load undergoes a conditioning treatment to bring its humidity and temperature levels suitable for more efficient penetration of the EtO gas inside the product and its packaging.
- EO Sterilization: Low-temperature sterilization by EtO / CO2 mixture injection at a pre-defined concentration.
- Post-conditioning/Degassing: Necessary to remove any EtO particles from the product and packaging. Degassing is performed with a series of alternating vacuums and inlets of air at a controlled temperature.
In the case of separate load cells, automatic loading/unloading systems are required allowing the operators to save time and avoid exposure to a potentially contaminated environment.
Highest industrial standards
A high-efficiency heating jacket surrounds Steelco's rectangular cross-section sterilization chamber for rapid and even heating of loads. The machine body is AISI 304 stainless steel, insulated with high-density ceramic material and a clad stainless steel sheet. The chamber and the hydraulic system are entirely built and clad stainless steel. Process piping is made of tri clamps and flange connections.
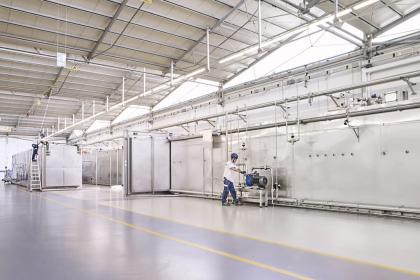
High productivity, low consumption
The new range of sterilizers has been designed for best-in-class energy recovery to optimize consumption. The vacuum system is provided with a water ring pump, supplied with water drawn from the separator by creating a closed circuit. The temperature is maintained at optimum levels by a heat exchanger. The pump outflow is directed to the separator, from where it is sent to the neutralizing system. The air supplied into the chamber in the degassing phase is filtered through absolute filters to guarantee higher quality.
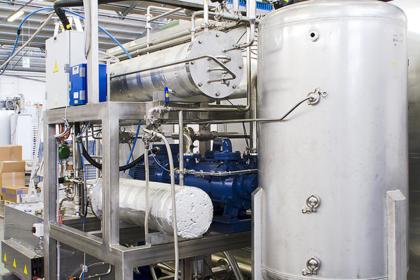
Complete enviroment protection
Effective and safe abatement of Ethylene Oxide at the completion of sterilization process by thermal combustion: increasingly stringent parameters make it necessary to offer safe accepted abatement systems on every Ethylene Oxide sterilizer. Steelco Group follows the ATEX, UL, OSHA, NFPA, and FDA regulations and complies with ISO 11135, EN 1422.